[ Chelating Resin Towers ]
Saturated brine to feed the membrane process for chlor-alcaly plants has to be super-purified in order to remove suspended solids and hardness at the level required by membrane manufacturers to prevent their rapid and irreversible damage.
Particularly, multivalent ions including Ca, Mg, Sr, Ba, Fe, Pb, Ni, Mu, Cr are responsible for the fouling of ion exchange membranes and therefore for their shorter life. The removal of such ions down to the required limits is done by passing the brine on beds of selective resins called chelating resins.
Unidro chelate resin systems are designed to obtain the very high treated brine quality which is to be achieved in the secondary brine purification units. Such units are normally installed as final step of the brine treatment trains, downstream the brine primary filters and brine secondary filters.
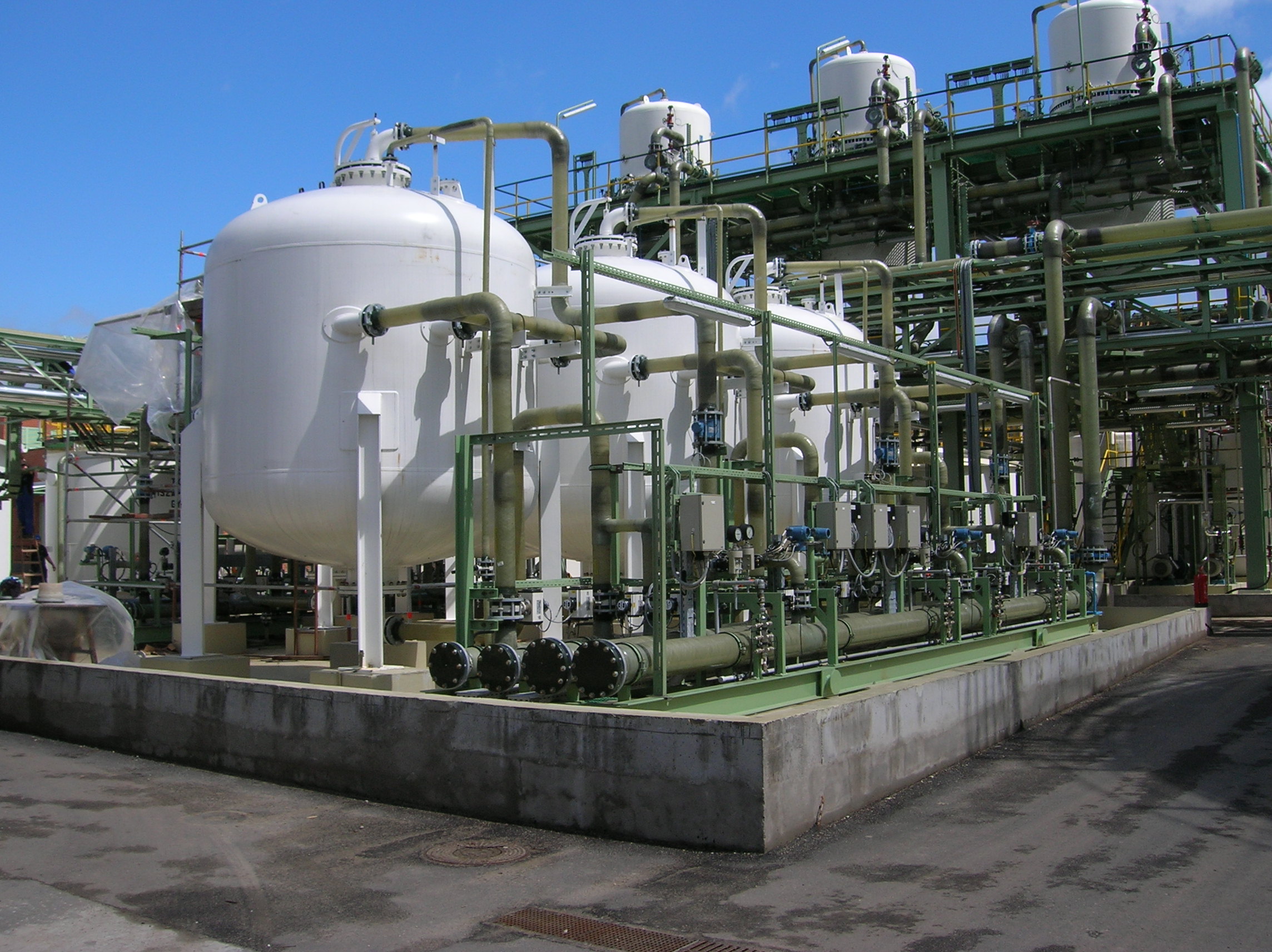
The systems consist of a double or triple towers train, resins regeneration units with acid and caustic, instruments and ON/OFF valves for a fully automatic operation.
The train arrangement of these systems is designed to ensure that the extremely low leakage of divalent ions can be obtained at any time. This requires a multiple columns system operating in the lead-lag mode. When the quality of the treated brine is very strict and the size of the unit requires a severe control of the chemical consumption, the most effective arrangement is a three columns system, operating in the so called merry-go-round mode.
When the design throughput of the lead column (first column) is reached, the column is put out of service and the regeneration sequence is initiated. During the regeneration the remaining tower(s) continue the operation and guarantee the same quality at outlet. Upon completion of the regeneration cycle, the column is put again into service in the polishing position (last column).
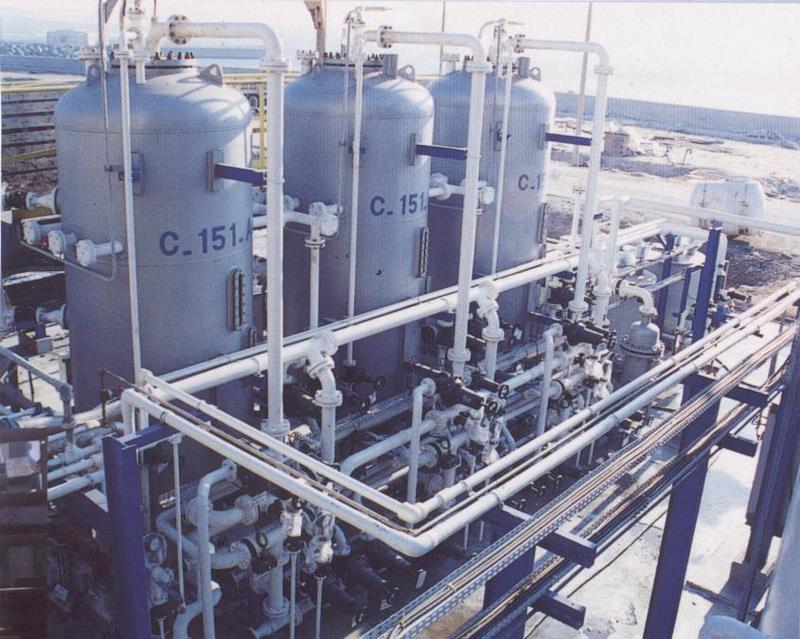
Unidro experience in the design and supply of chelate resin systems for chloralkali plants includes both two and three columns arrangement. Our know-how applies to all aspects which are critical for the performance of such units:
- the prevention of any by-passing or channelling phenomena in the resin bed which would lower the resin’s effective capacity (hardness leakage)
- the correct positioning and sizing of distributors
- the selection of flow rates during service and resin regeneration
All these aspects require an appropriate approach and a very accurate engineering design.
Another critical issue is the material selection which must take into account the fluid which is handled is hot saturated brine, chemically and physically very aggressive as well as very sensitive. Special lining for vessels internals, titanium for wet metallic parts, suitable non-metallic materials for specials are carefully selected to ensure performances and long-term reliability to the whole system.
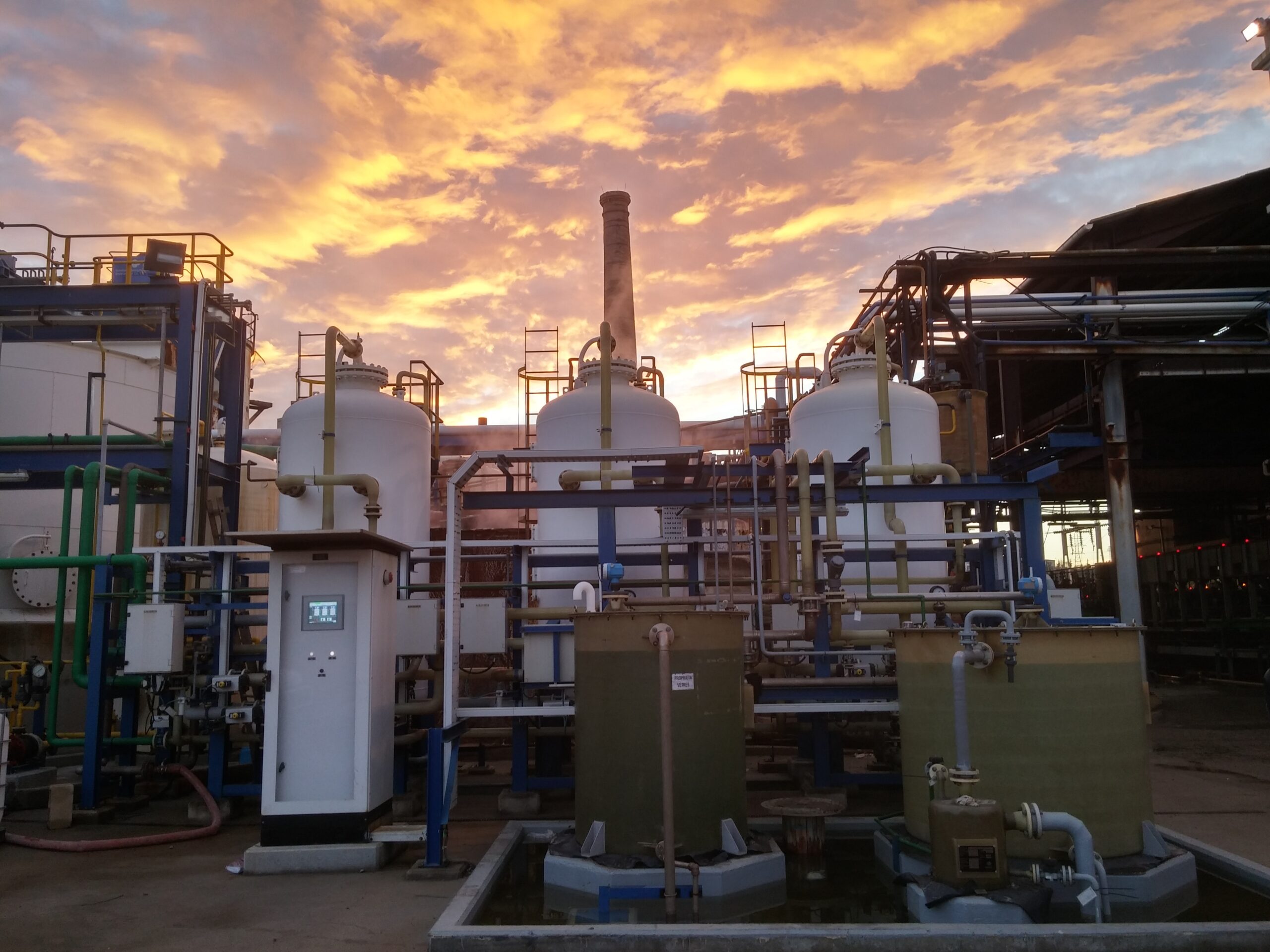